Run Better, Longer: Commercial Laundry Equipment Maintenance
As any seasoned operator knows, well-maintained machines are the lifeblood of the business, ensuring reliability, efficiency, and longevity. Because, let’s face it, a laundry business without working machines is just a room full of dirty laundry. Learn why routine maintenance is pivotal for your equipment and how Spin Techs Inc can be your ally in sustaining peak performance. From the daily checks to those all-important service calls, here’s how to keep your equipment running smoothly.
Why Maintenance is Key to Your Laundry Operations
Ever stopped to think about what really keeps your commercial laundry business running smoothly? Spoiler alert: it's not sheer luck. It's the hard work that goes into maintaining your laundry equipment. Here’s why maintenance matters more than you might think.
Reliability and Efficiency: Following maintenance routines protects against unexpected breakdowns, thereby preventing the dread of operational downtime. Less downtime means more laundry done. Simple.
Longevity of Equipment: Consistent care significantly extends the life span of your laundry equipment. While the average lifespan of a commercial washer lasts 10-15 years, regular maintenance can help extend its life to 20 years or more. This translates to cost savings over time, sparing you the frequent need for costly replacements.
Maintenance Tips for Optimal Equipment Performance
To keep your laundry operation running like a well-oiled machine, you’ll want to be proactive in your approach to maintenance. Here are a few best practices for optimizing your equipment:
Regular Cleaning Protocols
Dirt and grime are no friends of efficiency. Adherence to a disciplined cleaning schedule will help keep your machines operating at their best.
- Daily Exterior Wipe-Down: Clean all exterior surfaces of washers, dryers, and related equipment. This not only keeps the equipment looking professional but also prevents the buildup of daily grime.
- Weekly Interior Cleaning: Focus on the interior of washers including drums, gaskets, and dispensers, and for dryers, the lint traps and exhaust ducts. Consistent cleaning reduces buildup, which can affect performance, keeping machines efficient and free of odors.
- Monthly Deep Clean: Undertake a thorough cleaning of filters, water inlet hoses, and the venting system. Additionally, washers should have their drums and detergent dispensers cleaned deeply, while dryers need a focus on interior ducts, inverter drive system, and surfaces. This helps to identify wear or damage early and also prevents additional problems like an overheated motor control unit, which can cost you anywhere between $1,000-$3,0000. It also helps to conserve energy, leading to even more savings.
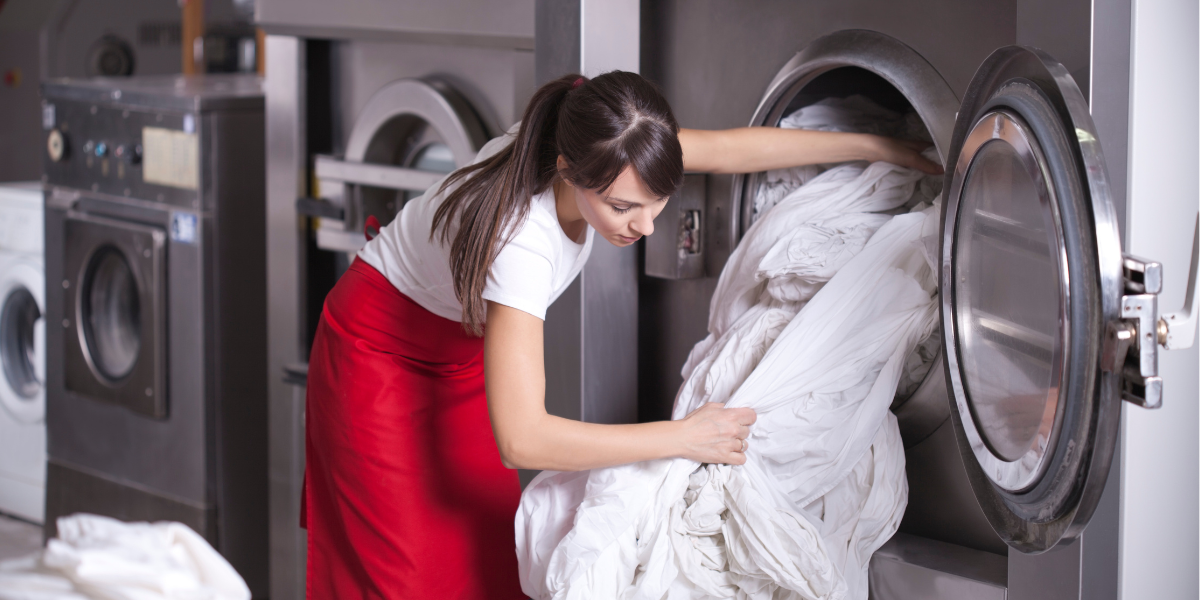
Regular commercial laundry equipment maintenance will help keep your machines running well.
Routine Inspections
Regular inspections unveil early signs of wear-and-tear, preventing minor issues from ballooning into expensive headaches. Below is a list of some of the key items that should be checked and what to look for.
Laundry Equipment Inspection List
Drum Bearings
Unusual noises during operation, especially during the spin cycle.
Belts
Cracks, fraying, or slack in the drive belts of washers and dryers.
Motors
Overheating, strange sounds, or burnt odors.
Water Inlet Valves
Proper water flow, signs of leakage, or mineral deposits which may indicate a malfunction.
Pump Operation
Effective drainage, unusual sounds, or water remaining in the drum.
Lint Traps and Exhaust Ducts
Clogging or lint accumulation in lint traps, and verify that exhaust ducts are clear.
Thermostats and Heating Elements (Dryers)
Proper heating performance and accuracy of temperature controls.
Control Panels and Buttons
Responsiveness and any signs of electrical issues or wear.
Shock Absorbers and Suspension (Washers)
Excessive vibration or movement during operation.
Door Seals and Gaskets
Leaks, tears, or mold build-up which can lead to leaks or reduce efficiency.
Water and Drain Hoses
Cracks, bulges, or leaks in both water supply and drainage hoses.
Filters
Debris, lint buildup, or obstructions in water and lint filters.
Ventilation System (Dryers)
Full airflow and no blockages in the venting path to the outside.
Floor Drain
Filter present and in good condition.
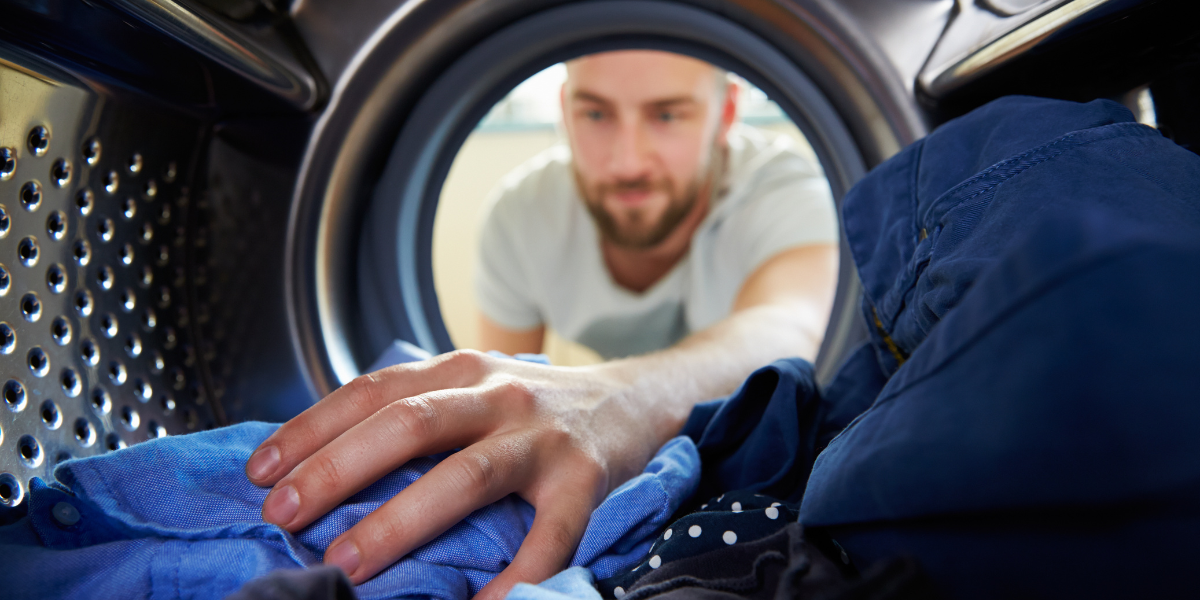
Laundry can be done in confidence when equipment is in good working condition due to regular maintenance.
Preventative Maintenance
Embracing a proactive approach to equipment care forestalls potential failures. Choosing the right professionals will help you safeguard your operation against unexpected downtimes. At Spin Techs, Inc, we understand the importance of a lost day, hour, or even minute. That’s why Spin Techs offers 24-hour emergency services, so your business remains uninterrupted. Coupled with extensive warranties that cover full parts for 3 to 5 years, choosing Spin Techs equates to choosing peace of mind.
Leave it to the Professionals: Why Trust Spin Techs with Your Laundry Equipment Decisions
Spin Techs Inc rises above the DIY approach, your average “fix-it” guy, and even big companies by offering professional, knowledgeable guidance tailored to your specific needs. Here are 10 reasons why Spin Techs' service is a step above the rest.
- Informed Decisions: Get expert advice on repairing or replacing - save on costs and prevent operational disruptions.
- Quality Brands: Choose from top brands like Yamamoto, Whirlpool, Fagor, and ADC.
- End-to-End Service: Access sales, maintenance, and support throughout your equipment's lifecycle - one partner for all your needs.
- 24-Hour Service Portal: Round-the-clock access to our service portal.
- Free Estimates: Plan better with no-cost evaluations for upgrading your equipment.
- Efficiency & Longevity: Benefit from our expertise to boost efficiency and extend machine life - save time and money.
- Reduced Downtime: Minimize disruptions with our reliable service - keep your business running smoothly.
- Energy Savings: Ensure your machines use less energy, thanks to optimal performance.
- Safety First: Trust the professionals to avoid any dangerous mistakes.
- Client Endorsements: Our success stories and testimonials speak for themselves.
Ready for smoother, longer lasting laundry operations? Contact Spin Techs Inc today. Let's discuss how our tailored solutions, dedicated support, and top-tier brands can elevate your business. Your efficiency, savings, and satisfaction are our priorities. Take the first step towards a seamless laundry management experience now.
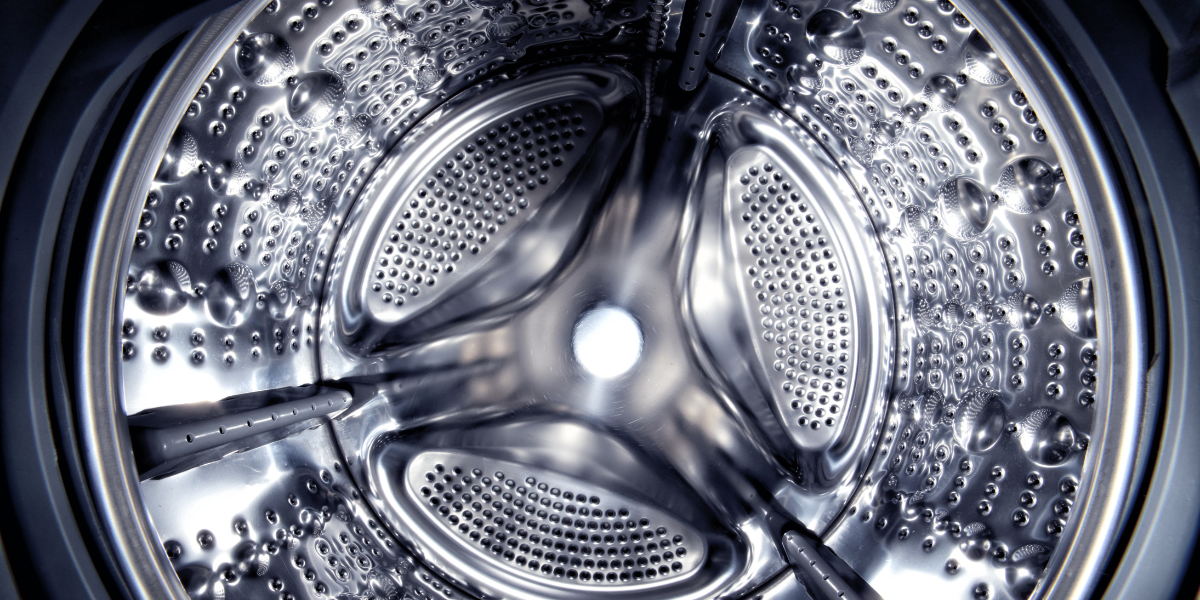
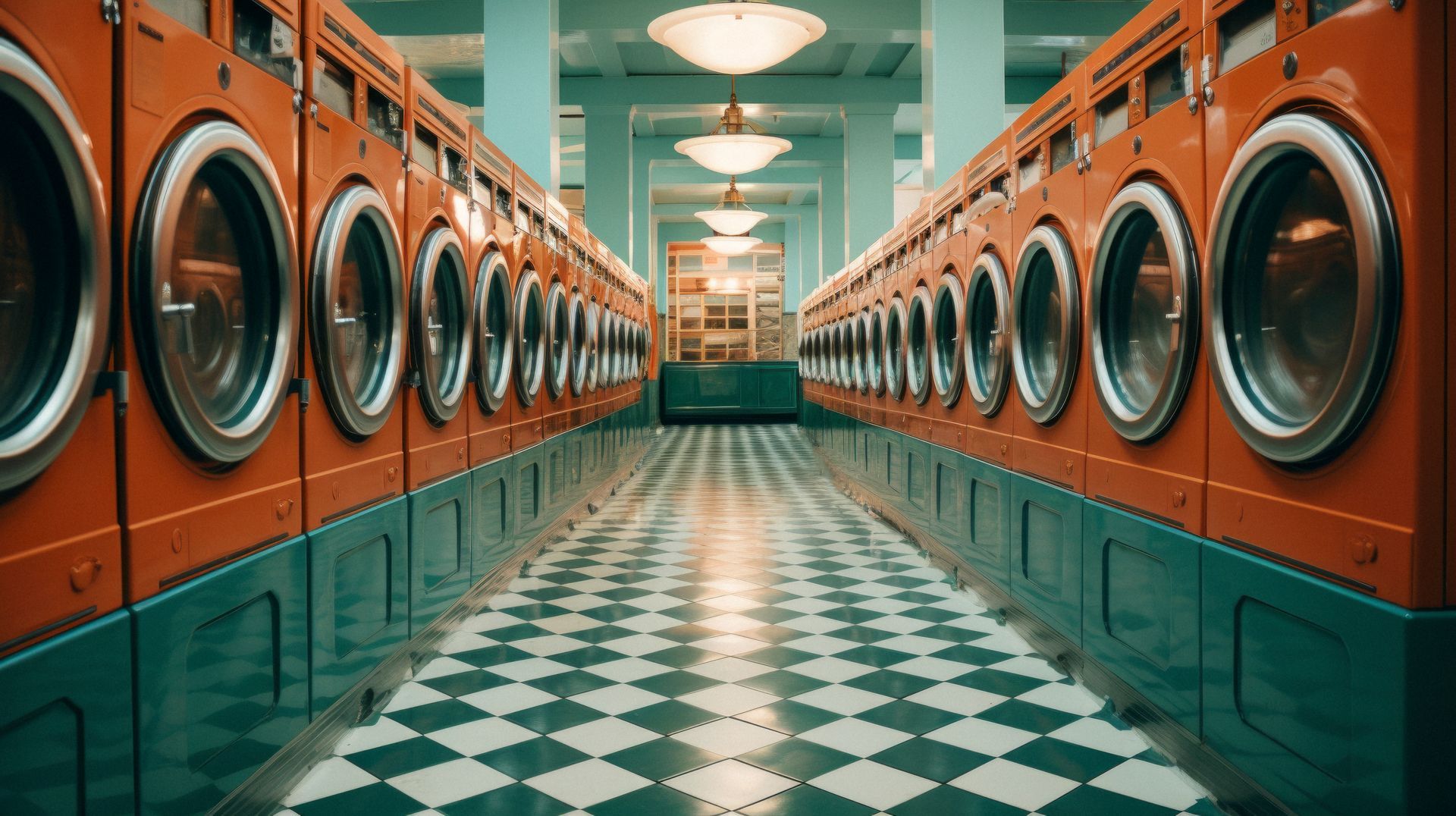
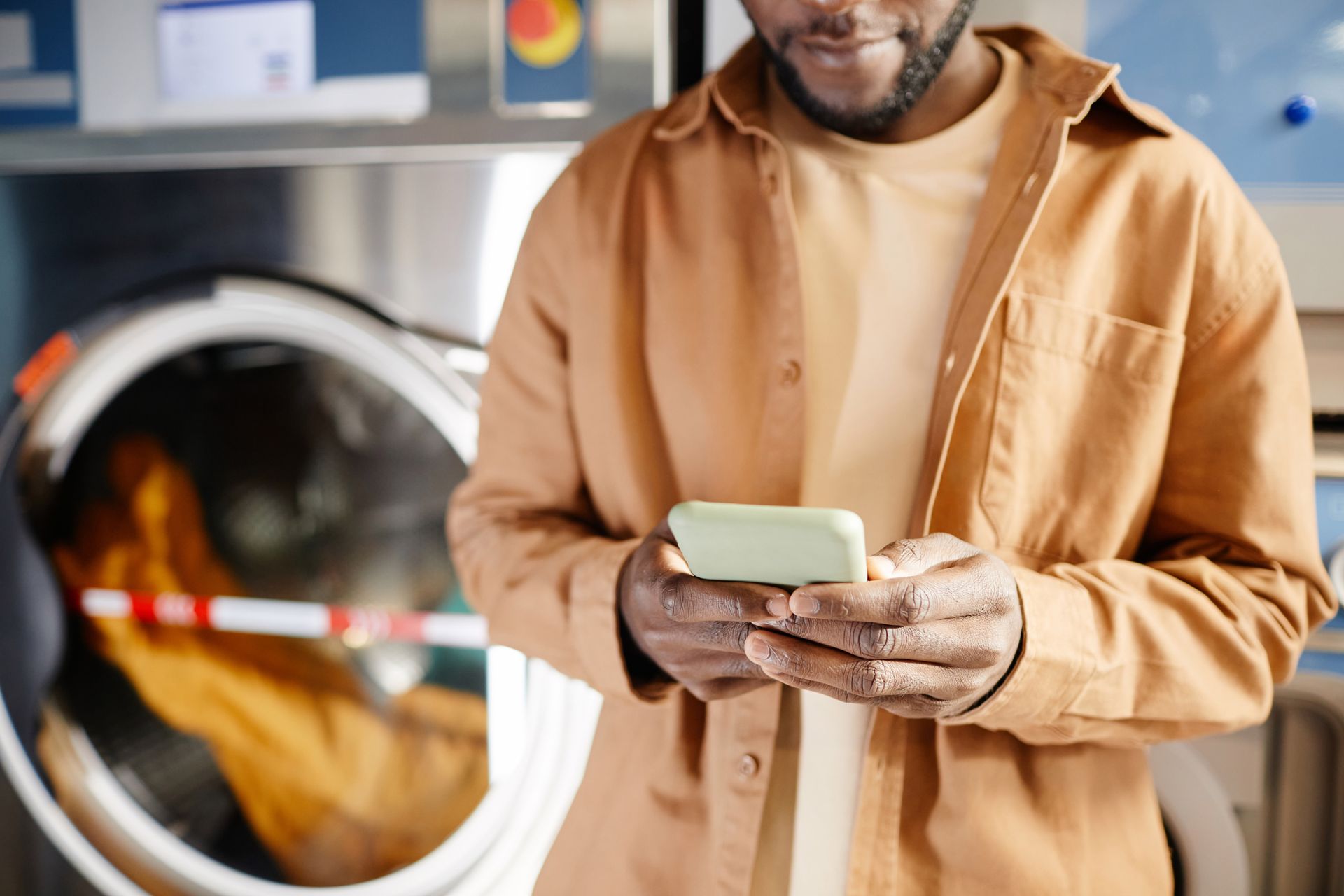
Share On: